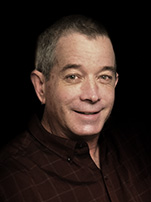
Servo Motors - What They Are and How They Work
by Paul Figie, Application Engineer, EZAutomation
Here is a little word history. The word servo “sər-vō” is derived from the Latin word “servus” meaning slave. The word motor “mō-dər” has its Latin origin “movere” to move, or “motor” mover. So we have “Slave Mover” meaning a command controlling an action or movement. This is a good starting point for an explanation as to what a servo motor is and how it works. First a signal or command is given to the device and device responds with the change in position. There are many types of servo motors and servomechanisms along with the control schemes that make them work. In a servo motion system there are three basic components a controller, an actuator and a position feedback device to the controller. Today’s automation applications demand speed and position accuracy and servo motor control systems have advanced to achieve the task. By using multipole motors and digital rotary encoders coupled with microprocessor technology servo motor control systems evolved to become better and more cost effective to implement. The diagrams bellow give the working concept for microprocessor AC servomotor controlling position, speed, and torque with a PLC.
Position Control Using a Pulse Signal The PLC inputs pulses for the destination position Encoder verifies the current position |
![]() |
![]() Position Control Diagram |
Speed Control by Analog Voltage Analog Voltage from PLC sets the speed |
![]() |
![]() Speed Control Diagram |
Torque Control by Analog Voltage Analog Voltage from the PLC limits the Torque |
![]() |
![]() Torque Control Diagram |
All three control loops work together to make up the complete system. When selecting your servo be sure to include all necessary I/O in PLC that will interface with the system you choose.