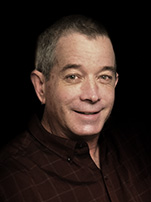
ABC’s of VFD’s Installation Need to Know (Part 2)
by Paul Figie, Application Engineer, EZAutomation
VFD’s PWM Technology
Most VFD’s today take advantage of high speed microprocessors to create the waveform output necessary to drive the motor being controlled. This is accomplished by switching outputs on and off at varying duty cycles called Pulse Width Modulation or PWM. The speed or frequency at which output is switched must be much greater than the frequency of the waveform that is being created this is called the modulation or carrier frequency. Depending on the output device configuration used in this switch process the carrier frequencies are generally between 1-20 KHz. The figure below gives an example of the microprocessor generated PWM and the waveform it creates.
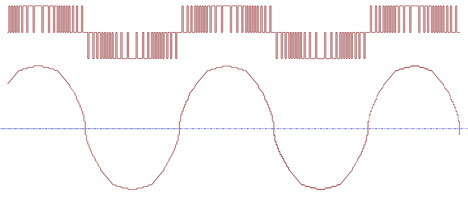
Generating PWM signals to control varying output frequencies has become very practical with the advancement of today’s Microprocessors. Microprocessor Controlled VFD’s have become very sophisticated in their control capabilities but not without some drawbacks. The high speed switching to create the output to the Motor generates Electromagnetic Interference (EMI). This EMI noise is inherent to all VFD’s using PWM and can be extremely problematic in your control system if extra steps are not taken to minimize it. Proper VFD installation is extremely important not only for the VFD and motor but also all other electrical devices in you control system. Improper VFD installation can not only cause damage to your motor and drive, but could cause erratic unpredictable and potentially dangerous conditions to surrounding electrical control devices.
1. VFD - Read the VFD Manufactures Drive Installation procedures. Pay close attention and follow all of the recommendations. This should include:
- a. VFD Mounting requirements to maintain proper heat dissipation and Electrical Noise isolation.
- b. Proper VFD and Motor grounding procedures.
- c. Motor wiring (Type of wire and method of routing) Metallic shielded with non-Metallic armored motor runs that are single point grounded on the VFD side are usually specified
- d. Allowable wire distance from the VFD to the Motor
- e. When the use of Line Reactors or Load Reactors may be required
- f. Motor overload protection for your specific motor and application.
- g. Your VFD should be in a separate enclosure from your PLC, HMI or other controls
2. Motor - Use Inverter Duty Motor type. Check that you are not exceeding manufactures performance recommendations.
- a. Note: not all Inverter duty motors are created equal. EMI noise within Induction motors has been known to induce currents on the rotor shaft that conduct through the motor bearings causing premature bearing failure. Some Motor manufactures insulate the bearing on one side of the rotor to alleviate this condition. EMI noise can cause voltage spikes within the motor that can break down its insulation within windings so higher insulation ratings are required.
- b. When mounting the Motor be sure the paint on the surfaces of the motor and the equipment it is mounted on is removed. This will allow a good electrical ground path.
3. Surrounding Equipment - VFD’s not only transmit electrical noise in proximity to the drive itself but also along the wiring run to the motor.
- a. Take extra care not to run any control signal wiring or communication wiring near your VFD, VFD Motor wire Runs or VFD Power runs. Running control or communication wiring in a parallel path to VFD runs can cause intermittent and erratic problems to other electric/electronic components that my not even be in proximity or related to your control system.
- b. VFD’s can reflect noise back into the sourcing power lines and should have a separate power source from any other control devices
- c. Be sure to follow all applicable electrical wiring codes and safe wiring practices
i. NEC “National Electric Code”
ii. IEC/EN 61800-3 “Adjustable Speed Electrical Power Drive“
iii. NEMA Standards Publication ICS 7.1-2000 “Safety Standards for Construction and Guide for Selection, Installation, and Operation of Adjustable-Speed Drive Systems
To make your VFD Drive installation successful upfront planning is key. Research and planning of your control system is always save time well spent.